Introduction:
Zircon, zirconia, and zirconium constitute a family of materials. Each of them has distinct properties and widespread applications. This exploration delves into their individual characteristics, applications, and pivotal roles across diverse industries and highlights their collective impact on modern technology and manufacturing. Hope that you can have a deep understanding.
Zircon:
Zircon is primarily composed of zirconium silicate. It boasts exceptional durability, heat resistance, and chemical inertness. Its applications span ceramics, refractories, and the production of zirconium compounds, serving as a foundational material in various sectors.
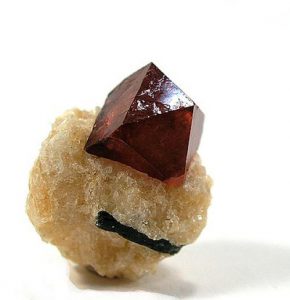
Zirconia (Zirconium Dioxide):
Zirconia is derived from zircon. It is also known as zirconium dioxide (ZrO2). ZrO2 exhibits remarkable strength, and thermal resistance, and finds widespread use in ceramics, and dental prosthetics. It serves as a refractory material across high-temperature industries as well.
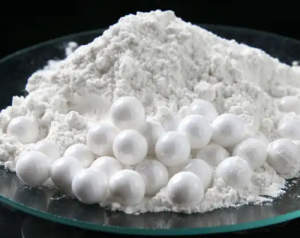
Zirconium:
Zirconium is an elemental metal extracted from zircon mineral sands. It showcases high corrosion resistance, low thermal neutron absorption, and compatibility with human tissues. Its uses extend to nuclear reactors, aerospace applications, and medical implants due to its exceptional properties.
Individual Significance and Applications:
Let’s continue with an extended breakdown of the individual characteristics of Zircon, Zirconia, and Zirconium. They have diverse attributes and pivotal roles across multiple industries, technological advancements, and materials science innovations.
1. Zircon’s Diverse Uses:
- Durability and Refractory Applications: Zircon’s resilience lends itself to manufacturing high-temperature ceramics, refractory materials, and foundry sands.
- Nuclear Industry: It is crucial in nuclear reactors because it has resistance to radiation and low thermal neutron absorption properties.
2. Applications of Zirconia:
- Mechanical Strength: Zirconia comes with strength and toughness. These properties render it valuable in dental prosthetics, engineering ceramics, and high-performance applications like ceramic knives.
- Biomedical Implants: Its biocompatibility makes it ideal for medical implants, especially in orthopedics and dental surgeries.
3. Zirconium’s Diverse Uses:
- Corrosion Resistance: Zirconium’s resistance to corrosion finds application in chemical processing equipment, aerospace components, and nuclear reactors.
- Biomedical Compatibility: This feature makes it a sought-after material for medical implants and prosthetics.
Other Compounds of Zirconium:
Zirconium also forms a myriad of compounds. Each of them comes with distinct properties and applications. Some notable compounds beyond zirconium dioxide (zirconia) include:
1. Zirconium Tetrachloride (ZrCl4):
Zirconium tetrachloride is a key precursor in zirconium chemistry. It serves as a vital reagent in various chemical processes. This compound’s role extends to catalysts and metal-organic frameworks (MOFs). It also serves as a reagent in the production of other zirconium compounds. All these uses mark its importance in industrial applications and research endeavors.
2. Zirconium Nitride (ZrN):
Zirconium nitride stands out for its impressive hardness, wear resistance, and golden appearance. So, it is used as a protective coating in the manufacturing of cutting tools. You can also find it as decorative coatings. It is also useful in the aerospace industry. Its ability to enhance the surface properties of materials contributes significantly to the durability and performance of various products.
3. Zirconium Hydroxide (Zr(OH)4):
Zirconium hydroxide is valued for its adsorption properties and chemical stability. It finds utility in water purification, catalysts, and as a precursor in the production of other zirconium compounds. Its role in environmental applications underscores its significance in addressing purification challenges.
Conclusion:
Zircon, zirconia, and zirconium form a trinity of materials. Each of them has distinct attributes and versatile applications. Their collective impact spans industries and drives innovation and advancements in ceramics, nuclear technology, medical sciences, and beyond. They are shaping the landscape of modern technology and paving the way for future developments.
Stanford Advanced Materials (SAM) now offers an extensive range of Zirconium products. Some of the Zirconium products available include zirconium metals, zirconium compounds, etc. Customized order is also welcome. Please contact for more information.
Reference:
[1] Zircon. (2023, November 22). In Wikipedia. https://en.wikipedia.org/wiki/Zircon