Properties of Zirconium
Zirconium easily absorbs hydrogen, nitrogen, and oxygen; zirconium has a strong affinity for oxygen, and oxygen dissolved in zirconium at 1000°C can significantly increase its volume. The surface of zirconium is easy to form an oxide film with luster, so its appearance is similar to that of steel. Zirconium is resistant to corrosion but is soluble in hydrofluoric acid and aqua regia. At high temperatures, zirconium can react with non-metallic elements and many metal elements to form solid solutions. Zirconium has good plasticity and is easy to be processed into plates, wires, etc. Zirconium can absorb a large amount of oxygen, hydrogen, nitrogen, and other gases when heated, and can be used as a hydrogen storage material. The corrosion resistance of zirconium is better than that of titanium, and it is close to niobium and tantalum. Zirconium and hafnium are two metals with similar chemical properties that are symbiotic together and contain radioactive substances.
Applications of Zirconium
Like lithium and titanium, zirconium can strongly absorb nitrogen, hydrogen, oxygen, and other gases. When the temperature exceeds 900 degrees Celsius, zirconium can absorb nitrogen violently; under the condition of 200 degrees Celsius, 100 grams of metal zirconium can absorb 817 liters of hydrogen, which is equivalent to more than 800,000 times that of iron. This characteristic of zirconium makes it widely used in the electric vacuum industry. People use zirconium powder to coat the surface of the anode and other heated parts of electric vacuum components and instruments to absorb residual gas in vacuum tubes. The high vacuum tubes and other electric vacuum instruments made in this way have high quality and long service life.
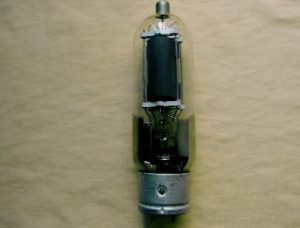
Zirconium has a small thermal neutron capture cross-section and has outstanding nuclear properties, so it is an indispensable material for the development of the atomic energy industry and can be used as a reactor core structural material. Zirconium powder is easy to burn in the air and can be used as a detonator and smokeless powder. Zirconium can be used as an additive for deoxidation and desulfurization of high-quality steel and is also a component of armor steel, cannon steel, stainless steel, and heat-resistant steel.
Zirconium can also be used as a “vitamin” in the metallurgical industry to exert its powerful deoxidation, nitrogen removal, and sulfur removal effects. Adding 1/1000 zirconium to steel will increase the hardness and strength amazingly; zirconium-containing armored steel, stainless steel, and heat-resistant steel are important materials for the manufacture of defense weapons such as armored vehicles, tanks, cannons, and bulletproof panels. When zirconium is mixed into copper and drawn into copper wire, the conductivity is not weakened, while the melting point is greatly improved, which is very suitable for high-voltage wires. Zirconium-containing zinc-magnesium alloy is light and resistant to high temperatures, and its strength is twice that of ordinary magnesium alloys. It can be used in the manufacture of jet engine components.
Zirconium powder is characterized by a low ignition point and fast burning speed and can be used as a primer for detonating detonators, which can explode even underwater. Zirconium powder plus oxidant is like adding fuel to the fire, it burns with strong light and dazzling, and it is a good material for making tracer and flare.
Zirconium alloys and their applications
Zirconium alloy is a non-ferrous alloy composed of zirconium as the matrix and other elements are added. The main alloying elements are tin, niobium, iron, and so on. Zirconium alloy has good corrosion resistance, moderate mechanical properties, low atomic thermal neutron absorption cross-section in high temperature and high-pressure water and steam at 300-400 °C, and has good compatibility with nuclear fuel. In addition, zirconium alloy has excellent corrosion resistance to various acids, alkalis, and salts, and has a strong affinity with oxygen, nitrogen, and other gases, so it is also used in the manufacture of corrosion-resistant parts and pharmaceutical machinery parts. For example, it is widely used as a non-evaporable getter in the electric vacuum and light bulb industries.
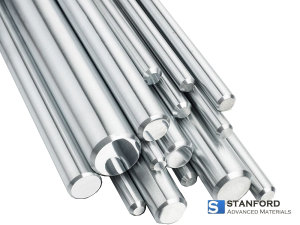
There are two types of zirconium alloys produced on an industrial scale: the zirconium-tin series and the zirconium-niobium series. The former alloy grades are Zr-2 and Zr-4, and the typical representative of the latter is Zr-2.5Nb. In zirconium-tin alloys, the alloying elements tin, iron, chromium, and nickel can improve the strength, corrosion resistance, and thermal conductivity of the corrosion-resistant film, and reduce the sensitivity of the surface state to corrosion. Usually, Zr-2 alloys are used in boiling water reactors, and Zr-4 alloys are used in pressurized water reactors. In zirconium-niobium-based alloys, the corrosion resistance of the alloy is the best when the addition amount of niobium reaches the solid solution limit of the crystal structure of zirconium at the service temperature. Zirconium alloy has isomorphous transformation, the crystal structure is body-centered cubic at high temperature, and hexagonal close-packed at low temperature. Zirconium alloy has good plasticity and can be made into pipes, plates, bars and wires by plastic processing; its weldability is also good and can be used for welding.
Other Zirconium Compounds
Zirconium dioxide and zircon are the most valuable compounds in refractory materials. Zirconium dioxide is the main material of new ceramics and cannot be used as a heating material that resists high-temperature oxidation. Zirconium dioxide can be used as an additive for acid-resistant enamel and glass, which can significantly improve the elasticity, chemical stability, and heat resistance of glass. Zircon has a strong light reflection performance and good thermal stability and can be used as sunscreen in ceramics and glass. Zirconium can absorb a large amount of oxygen, hydrogen, ammonia, and other gases when heated, and is an ideal getter. For example, zirconium powder is used as a degassing agent in electronic tubes, and zirconium wire and zirconium sheets are used as grid supports and anode supports.
Powdered iron mixed with zirconium nitrate can be used as glitter powder. Zirconium metal is used almost exclusively as the cladding for uranium fuel elements in nuclear reactors. It is also used to make photographic flashes, as well as corrosion-resistant containers and pipes, especially hydrochloric and sulfuric acids. Zirconium chemicals can be used as crosslinking agents for polymers.
For more information, please visit https://www.samaterials.com/.